DIY Table Upgrades
-
- Posts: 90
- Joined: Mon Jun 24, 2019 3:30 pm
- Acorn CNC Controller: Yes
- Allin1DC CNC Controller: No
- Oak CNC controller: No
- CNC Control System Serial Number: none
- DC3IOB: No
- CNC12: Yes
- CNC11: No
- CPU10 or CPU7: No
DIY Table Upgrades
I started a New Build topic back in July of 2022. I've used the table since then to make usable parts but the quality has been lacking.
https://centroidcncforum.com/viewtopic.php?t=7463
I'm starting a new Upgrade Topic because I finally got a new to me Powermax 45XP that was built in July of 2021. It has the CPC port and voltage divider but came with a hand torch. I plan to use the hand torch for now without THC but would like to upgrade to a machine torch and Acorn THC at some point in the future.
I have read some post on other forums that the 45XP won't fire a hand torch through the CPC port. Some users have bypassed the lockout by adding a switch wired to the inside of the unit. Others have swapped pins in the quick connect to make the unit think it has a machine torch. I haven't been able to find a reliable schematic for the 45XP showing the torch wiring. I don't want to modify the internals so I would go the swapping pins route but would like to verify what I'm reading.
So to make a long post short (too late), has anyone made the change to use a hand torch on the 45XP?
Mark
https://centroidcncforum.com/viewtopic.php?t=7463
I'm starting a new Upgrade Topic because I finally got a new to me Powermax 45XP that was built in July of 2021. It has the CPC port and voltage divider but came with a hand torch. I plan to use the hand torch for now without THC but would like to upgrade to a machine torch and Acorn THC at some point in the future.
I have read some post on other forums that the 45XP won't fire a hand torch through the CPC port. Some users have bypassed the lockout by adding a switch wired to the inside of the unit. Others have swapped pins in the quick connect to make the unit think it has a machine torch. I haven't been able to find a reliable schematic for the 45XP showing the torch wiring. I don't want to modify the internals so I would go the swapping pins route but would like to verify what I'm reading.
So to make a long post short (too late), has anyone made the change to use a hand torch on the 45XP?
Mark
-
- Posts: 90
- Joined: Mon Jun 24, 2019 3:30 pm
- Acorn CNC Controller: Yes
- Allin1DC CNC Controller: No
- Oak CNC controller: No
- CNC Control System Serial Number: none
- DC3IOB: No
- CNC12: Yes
- CNC11: No
- CPU10 or CPU7: No
Re: DIY Table Upgrades
I gave up on the idea of using the hand torch in favor of purchasing a Hypertherm machine torch. It's probably overkill for my needs but why go half way 
Torch mount pictures added to end of Google photo album.

Torch mount pictures added to end of Google photo album.
-
- Posts: 533
- Joined: Tue Aug 17, 2021 10:51 am
- Acorn CNC Controller: Yes
- Allin1DC CNC Controller: No
- Oak CNC controller: No
- CNC Control System Serial Number: none
- DC3IOB: No
- CNC12: Yes
- CNC11: No
- CPU10 or CPU7: No
Re: DIY Table Upgrades
Hi Mark,
The new torch looks Slick!
Did you hook up the ARC OK signal from the 45XP?
If not that will help improve Pierce delay accuracy.
Can you throw up a fresh report?
Nice work with the gearboxes also!
The new torch looks Slick!
Did you hook up the ARC OK signal from the 45XP?
If not that will help improve Pierce delay accuracy.
Can you throw up a fresh report?
Nice work with the gearboxes also!
-
- Posts: 90
- Joined: Mon Jun 24, 2019 3:30 pm
- Acorn CNC Controller: Yes
- Allin1DC CNC Controller: No
- Oak CNC controller: No
- CNC Control System Serial Number: none
- DC3IOB: No
- CNC12: Yes
- CNC11: No
- CPU10 or CPU7: No
Re: DIY Table Upgrades
Thanks Joey,
I did connect the Arc OK to input 5. I made a test cut last night using the 4" test file included with CNC12.I was blown away by the cut quality. There was absolutely no dross
. I added the pictures to my Google album.
I did connect the Arc OK to input 5. I made a test cut last night using the 4" test file included with CNC12.I was blown away by the cut quality. There was absolutely no dross

-
- Posts: 90
- Joined: Mon Jun 24, 2019 3:30 pm
- Acorn CNC Controller: Yes
- Allin1DC CNC Controller: No
- Oak CNC controller: No
- CNC Control System Serial Number: none
- DC3IOB: No
- CNC12: Yes
- CNC11: No
- CPU10 or CPU7: No
Re: DIY Table Upgrades
I got this 2 sensor round torch mount. I didn't get their sensors so I could get better sensors.
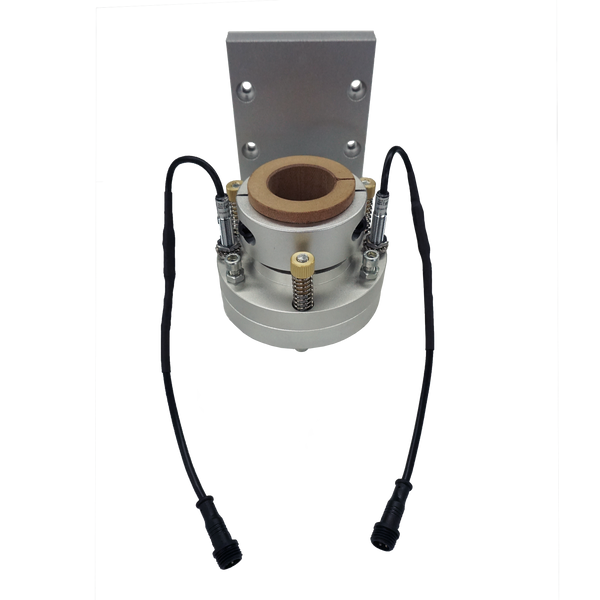
Hookup schematic S15123.r2 shows one sensor used for the TorchFloatSwitch and the other one for the TorchBreakawayOK switch. I read that the TorchFloatSwitch will be used for TorchBreakawayOK if triggered outside of a touchoff operation. Therefore wouldn't it be better to connect both sensors as TorchFloatSwitchs?
What is the best sensor to use for detecting aluminum?
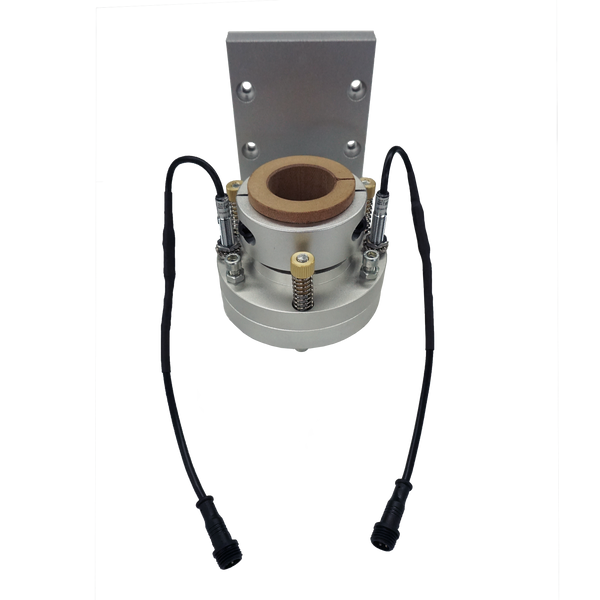
Hookup schematic S15123.r2 shows one sensor used for the TorchFloatSwitch and the other one for the TorchBreakawayOK switch. I read that the TorchFloatSwitch will be used for TorchBreakawayOK if triggered outside of a touchoff operation. Therefore wouldn't it be better to connect both sensors as TorchFloatSwitchs?
What is the best sensor to use for detecting aluminum?
-
- Posts: 90
- Joined: Mon Jun 24, 2019 3:30 pm
- Acorn CNC Controller: Yes
- Allin1DC CNC Controller: No
- Oak CNC controller: No
- CNC Control System Serial Number: none
- DC3IOB: No
- CNC12: Yes
- CNC11: No
- CPU10 or CPU7: No
Re: DIY Table Upgrades
Please help. Touch off and torch breakaway not working.
I got 2 Micro Detectors AES-CN-1F proximity sensors for my new round mount. They are NPN NC switches. https://www.automationdirect.com/adc/sh ... /aes-cn-1f
They are wired according to schematic S15123 ( https://www.centroidcnc.com/dealersuppo ... 123.r2.pdf). One sensor is configured as a TorchFloatSwitch connected to input 4. The other sensor is configured as a TorchBreakawayOK connected to input 7 with the input inverted. The TorchFloatSwitch is configured in the wizard as the only touch off method. The input state when triggered is closed.
The torch touch off button will move the torch down and touch the surface and start to reverse to the safe height. However, it fails prior to reaching the retract height. I tried other configurations but nothing worked correctly.
A report file is attached.
I got 2 Micro Detectors AES-CN-1F proximity sensors for my new round mount. They are NPN NC switches. https://www.automationdirect.com/adc/sh ... /aes-cn-1f
They are wired according to schematic S15123 ( https://www.centroidcnc.com/dealersuppo ... 123.r2.pdf). One sensor is configured as a TorchFloatSwitch connected to input 4. The other sensor is configured as a TorchBreakawayOK connected to input 7 with the input inverted. The TorchFloatSwitch is configured in the wizard as the only touch off method. The input state when triggered is closed.
The torch touch off button will move the torch down and touch the surface and start to reverse to the safe height. However, it fails prior to reaching the retract height. I tried other configurations but nothing worked correctly.
A report file is attached.
- Attachments
-
- report_3484E41BC6EB-0511226197_2023-11-17_16-08-20.zip
- (5.67 MiB) Downloaded 75 times
-
- Posts: 533
- Joined: Tue Aug 17, 2021 10:51 am
- Acorn CNC Controller: Yes
- Allin1DC CNC Controller: No
- Oak CNC controller: No
- CNC Control System Serial Number: none
- DC3IOB: No
- CNC12: Yes
- CNC11: No
- CPU10 or CPU7: No
Re: DIY Table Upgrades
Just wire both proximity switches as float switches and remove the breakaway.
If the Float switch trips outside of a touch off cycle it will be treated as a breakaway.
So you still will have the breakaway switch functionality.
If the Float switch trips outside of a touch off cycle it will be treated as a breakaway.
So you still will have the breakaway switch functionality.
-
- Posts: 90
- Joined: Mon Jun 24, 2019 3:30 pm
- Acorn CNC Controller: Yes
- Allin1DC CNC Controller: No
- Oak CNC controller: No
- CNC Control System Serial Number: none
- DC3IOB: No
- CNC12: Yes
- CNC11: No
- CPU10 or CPU7: No
Re: DIY Table Upgrades
Thanks Joey. I wired both sensors in parallel and connected them to input 4 defined as TorchFloatSwitch. It appears that Touchoff and Breakaway are both working.
With the breakaway configuration, the machine is less tolerant to warped material. Now I see the need for THC even more than before. My X&Y axes have a OTR of 1.59155. I am able to reliably get 500 IPM movement. The Z axis however has a OTR of 6.042479 and only 100 IMP reliable movement. Would the THC work okay with this configuration?
With the breakaway configuration, the machine is less tolerant to warped material. Now I see the need for THC even more than before. My X&Y axes have a OTR of 1.59155. I am able to reliably get 500 IPM movement. The Z axis however has a OTR of 6.042479 and only 100 IMP reliable movement. Would the THC work okay with this configuration?
-
- Posts: 2372
- Joined: Fri May 24, 2019 8:34 am
- Acorn CNC Controller: Yes
- Allin1DC CNC Controller: No
- Oak CNC controller: No
- CNC Control System Serial Number: 7804734C6498-0401191832
- DC3IOB: No
- CNC12: Yes
- CNC11: No
- CPU10 or CPU7: No
- Location: Clearwater, FL
Re: DIY Table Upgrades
Correct me if I'm wrong here but they should be wired in series so if either one trips it triggers the circuit. Not both. If you have them wired in parallel it'll take BOTH being tripped to trigger a "breakaway" outside of the touch off command. So I'd be careful right now as it'll take a lot to trip a breakaway while cutting. You don't want to break a torch.
Cutting thin material almost requires THC as it warps all by itself at any given time. It's really cool to see the torch jump and follow the warps when cutting.

Cutting thin material almost requires THC as it warps all by itself at any given time. It's really cool to see the torch jump and follow the warps when cutting.
-
- Posts: 90
- Joined: Mon Jun 24, 2019 3:30 pm
- Acorn CNC Controller: Yes
- Allin1DC CNC Controller: No
- Oak CNC controller: No
- CNC Control System Serial Number: none
- DC3IOB: No
- CNC12: Yes
- CNC11: No
- CPU10 or CPU7: No
Re: DIY Table Upgrades
That's what I thought too. But schematic S15124 shows 2 sensors on a 3 sensor round mount being wired in parallel configured as Breakaway. I also tested it and either sensor tripped alone will signal a Breakaway. I had to configure "The input state when triggered is closed" in the wizard.