Hi,
I'm having problems with parting on my little DIY ATC, it struggles to do parting.
Can I mount a parting blade on the opposite side of the ATC and then part with X inverted? I assume its possible, gang setup etc seems to allow this. Looking at the manual, there are options for reversing spindle direction and 'entry' point might allow this? My key question is whether it then knows that X is flipped around (ie, 0 is now towards me, not away from me).
Thanks
ATC + Manual Gang
Moderator: cnckeith
-
- Posts: 2190
- Joined: Sat Nov 18, 2017 2:32 pm
- Acorn CNC Controller: Yes
- Plasma CNC Controller: No
- AcornSix CNC Controller: Yes
- Allin1DC CNC Controller: No
- Hickory CNC Controller: No
- Oak CNC controller: No
- CNC Control System Serial Number: Acorn 238
- DC3IOB: No
- CNC12: Yes
- CNC11: No
- CPU10 or CPU7: No
- Location: Bergland, MI, USA
- Contact:
Re: ATC + Manual Gang
Chaz...
Can you explain your problem a little more? What makes you think that a rear approach will solve the issue?
Can you explain your problem a little more? What makes you think that a rear approach will solve the issue?
-
- Posts: 392
- Joined: Thu Feb 08, 2018 7:57 am
- Acorn CNC Controller: No
- Allin1DC CNC Controller: No
- Oak CNC controller: No
- CNC Control System Serial Number: none
- DC3IOB: No
- CNC11: No
- CPU10 or CPU7: No
Re: ATC + Manual Gang
I have an ATC which struggles to deal with the flex/stress of parting. Its OK for anything up to around 25mm in Diameter in Alu. The design of the ratchet / pawl is not good, Ill sort this in time.Gary Campbell wrote: ↑Sun Sep 16, 2018 9:00 am Chaz...
Can you explain your problem a little more? What makes you think that a rear approach will solve the issue?
So I was thinking to mount a hard mounted manual tool change holder and put the Parting Blade in that for better parting.
So ATC is mounted closest to operator, manual parting is mounted opposite side. Can I use both?
-
- Posts: 392
- Joined: Thu Feb 08, 2018 7:57 am
- Acorn CNC Controller: No
- Allin1DC CNC Controller: No
- Oak CNC controller: No
- CNC Control System Serial Number: none
- DC3IOB: No
- CNC11: No
- CPU10 or CPU7: No
Re: ATC + Manual Gang
https://youtu.be/K5xjzFy8vEY?t=17m10s here you can see a tool that comes in from the left and right of the X Axis.
-
- Posts: 237
- Joined: Mon Nov 20, 2017 10:13 am
- Acorn CNC Controller: Yes
- Allin1DC CNC Controller: No
- Oak CNC controller: No
- CNC Control System Serial Number: none
- DC3IOB: No
- CNC11: Yes
- CPU10 or CPU7: Yes
- Location: Frenchville, PA
Re: ATC + Manual Gang
Chaz,
Yes to the question of having an ATC and gang tool post. You would call a station on the ATC and use a different offset for the gang tool(s) Example: for a 4 station ATC normally you would call T0404 for tool 4 with 04 offset. For the gang tool you would use Tool 4 station with 05 offset. For the Gang tool you would call T0405. When setting up the gang tool in the Tool Library in the "Tool Loc" column curser down and change T05 to T04. Now you will use off.# 5 to set the tool. This can be done this way for more than 1 gang tool with an ATC. You assign a Tool Loc with a different tool offset number for the gang tool. The example uses tool location 4 with offset 5. You can use any tool location that is on the turret with any offset that is not already used for a gang offset.
Make sure the spindle direction is correct for how you have the gang tool set up from the rear. If the ATC is mounted on the rear you can mount the gang tool on the front and do the same thing. I understand why you need to mount the tool as a gang tool to get it rigid.
For setting the X for the gang tool the "X Diam:" for the rear mount gang tooling you will use a negative X. Set the tool from the backside of the material. All the moves for the gang tool will be negative X instead of a positive X for the moves. Also for a tool change you want to make clearance moves in Z before you do a tool change to make sure the Gang tool will clear the end of the part.
Chaz wrote: ↑Sun Sep 16, 2018 7:59 am Can I mount a parting blade on the opposite side of the ATC and then part with X inverted? I assume its possible, gang setup etc seems to allow this. Looking at the manual, there are options for reversing spindle direction and 'entry' point might allow this? My key question is whether it then knows that X is flipped around (ie, 0 is now towards me, not away from me).
Yes to the question of having an ATC and gang tool post. You would call a station on the ATC and use a different offset for the gang tool(s) Example: for a 4 station ATC normally you would call T0404 for tool 4 with 04 offset. For the gang tool you would use Tool 4 station with 05 offset. For the Gang tool you would call T0405. When setting up the gang tool in the Tool Library in the "Tool Loc" column curser down and change T05 to T04. Now you will use off.# 5 to set the tool. This can be done this way for more than 1 gang tool with an ATC. You assign a Tool Loc with a different tool offset number for the gang tool. The example uses tool location 4 with offset 5. You can use any tool location that is on the turret with any offset that is not already used for a gang offset.
Make sure the spindle direction is correct for how you have the gang tool set up from the rear. If the ATC is mounted on the rear you can mount the gang tool on the front and do the same thing. I understand why you need to mount the tool as a gang tool to get it rigid.
For setting the X for the gang tool the "X Diam:" for the rear mount gang tooling you will use a negative X. Set the tool from the backside of the material. All the moves for the gang tool will be negative X instead of a positive X for the moves. Also for a tool change you want to make clearance moves in Z before you do a tool change to make sure the Gang tool will clear the end of the part.
Dana
When requesting support, please ALWAYS post a current report.
Need support? READ THIS POST first. http://centroidcncforum.com/viewtopic.php?f=60&t=1043
All Acorn Documentation is located here: viewtopic.php?f=60&t=3397
Answers to common questions: viewforum.php?f=63
and here viewforum.php?f=61
When requesting support, please ALWAYS post a current report.
Need support? READ THIS POST first. http://centroidcncforum.com/viewtopic.php?f=60&t=1043
All Acorn Documentation is located here: viewtopic.php?f=60&t=3397
Answers to common questions: viewforum.php?f=63
and here viewforum.php?f=61
-
- Posts: 392
- Joined: Thu Feb 08, 2018 7:57 am
- Acorn CNC Controller: No
- Allin1DC CNC Controller: No
- Oak CNC controller: No
- CNC Control System Serial Number: none
- DC3IOB: No
- CNC11: No
- CPU10 or CPU7: No
Re: ATC + Manual Gang
Great, thanks. Need to look at some practical things to make it work but looks to be viable. Appreciated.cnc_smith wrote: ↑Mon Sep 17, 2018 5:08 pm Chaz,
Chaz wrote: ↑Sun Sep 16, 2018 7:59 am Can I mount a parting blade on the opposite side of the ATC and then part with X inverted? I assume its possible, gang setup etc seems to allow this. Looking at the manual, there are options for reversing spindle direction and 'entry' point might allow this? My key question is whether it then knows that X is flipped around (ie, 0 is now towards me, not away from me).
Yes to the question of having an ATC and gang tool post. You would call a station on the ATC and use a different offset for the gang tool(s) Example: for a 4 station ATC normally you would call T0404 for tool 4 with 04 offset. For the gang tool you would use Tool 4 station with 05 offset. For the Gang tool you would call T0405. When setting up the gang tool in the Tool Library in the "Tool Loc" column curser down and change T05 to T04. Now you will use off.# 5 to set the tool. This can be done this way for more than 1 gang tool with an ATC. You assign a Tool Loc with a different tool offset number for the gang tool. The example uses tool location 4 with offset 5. You can use any tool location that is on the turret with any offset that is not already used for a gang offset.
Make sure the spindle direction is correct for how you have the gang tool set up from the rear. If the ATC is mounted on the rear you can mount the gang tool on the front and do the same thing. I understand why you need to mount the tool as a gang tool to get it rigid.
For setting the X for the gang tool the "X Diam:" for the rear mount gang tooling you will use a negative X. Set the tool from the backside of the material. All the moves for the gang tool will be negative X instead of a positive X for the moves. Also for a tool change you want to make clearance moves in Z before you do a tool change to make sure the Gang tool will clear the end of the part.
-
- Posts: 392
- Joined: Thu Feb 08, 2018 7:57 am
- Acorn CNC Controller: No
- Allin1DC CNC Controller: No
- Oak CNC controller: No
- CNC Control System Serial Number: none
- DC3IOB: No
- CNC11: No
- CPU10 or CPU7: No
Re: ATC + Manual Gang
So, tried to get this working over the weekend but no go.
First thing, set parameter for Gang Tooling = 1. So now I have rear as an option.
The problem that I have is that the X never flips over. First, below is a pic of my lathe's orientation. Ignore the temp nature of the gang tooling, just for visual representation. Tool turret at the bottom, gang at the top.
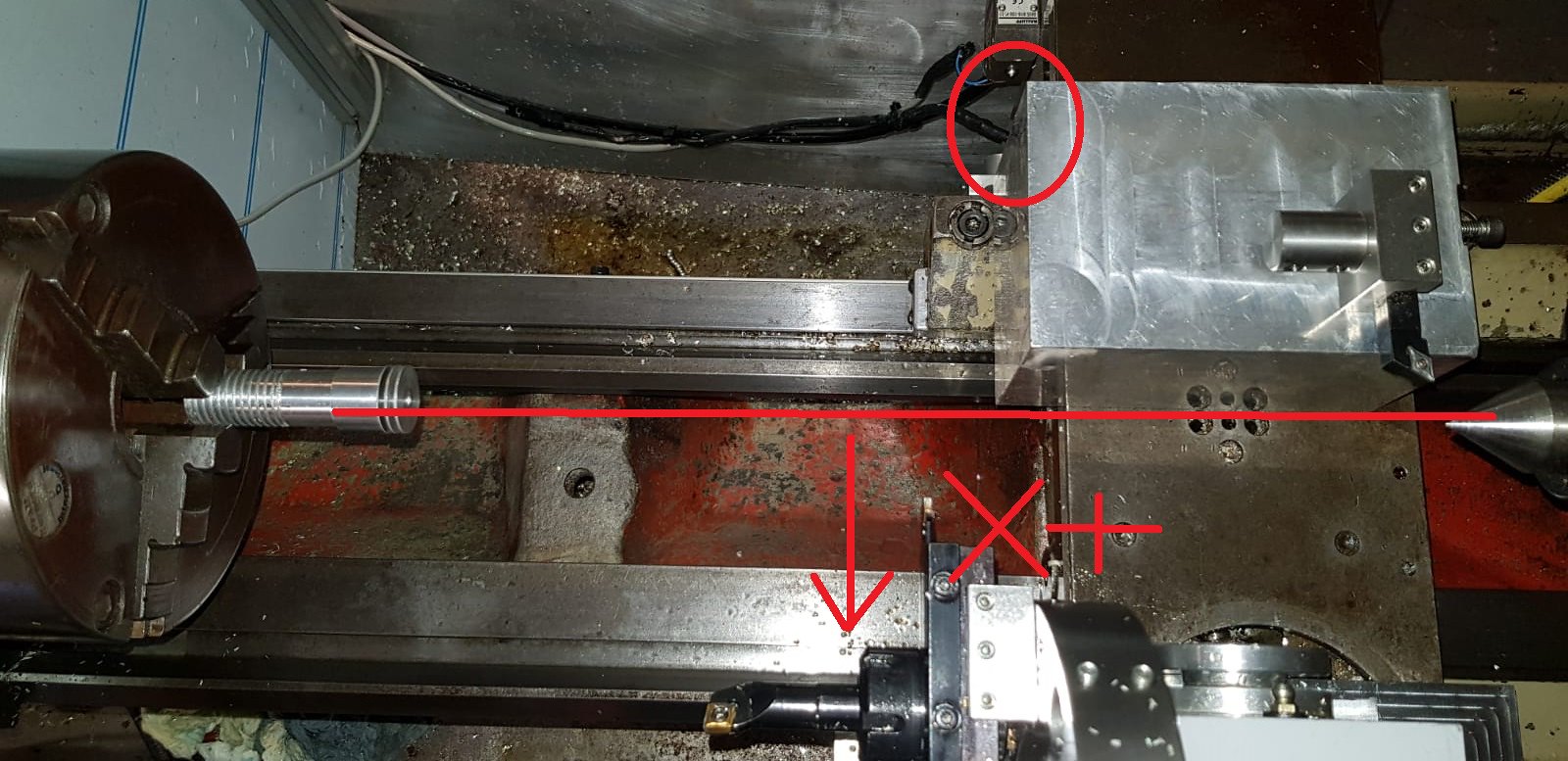
I home the machine to the home switch at the top (red circle) which means that the X is in its most positive direction. My offsets are all negative (basically my offsets are from machine 0, not sure if this is an issue.
I also noted that Parameter 1 allows a modification to the machine layout. Mine was parameter = 1. It says then to allow X to flip, add 2 to the amount (so use Parameter 1 = 3). I did this too, no change. Do I need to restart the system (Acorn) before these changes take effect?

I tried various options, tool 3 offset 9. What I did not try (another thread refers to it) was to bluff saying that its an ID tool, not OD. I tried Rear Approach, vector 6 and 8. The X doesnt switch over, no matter what I tried.
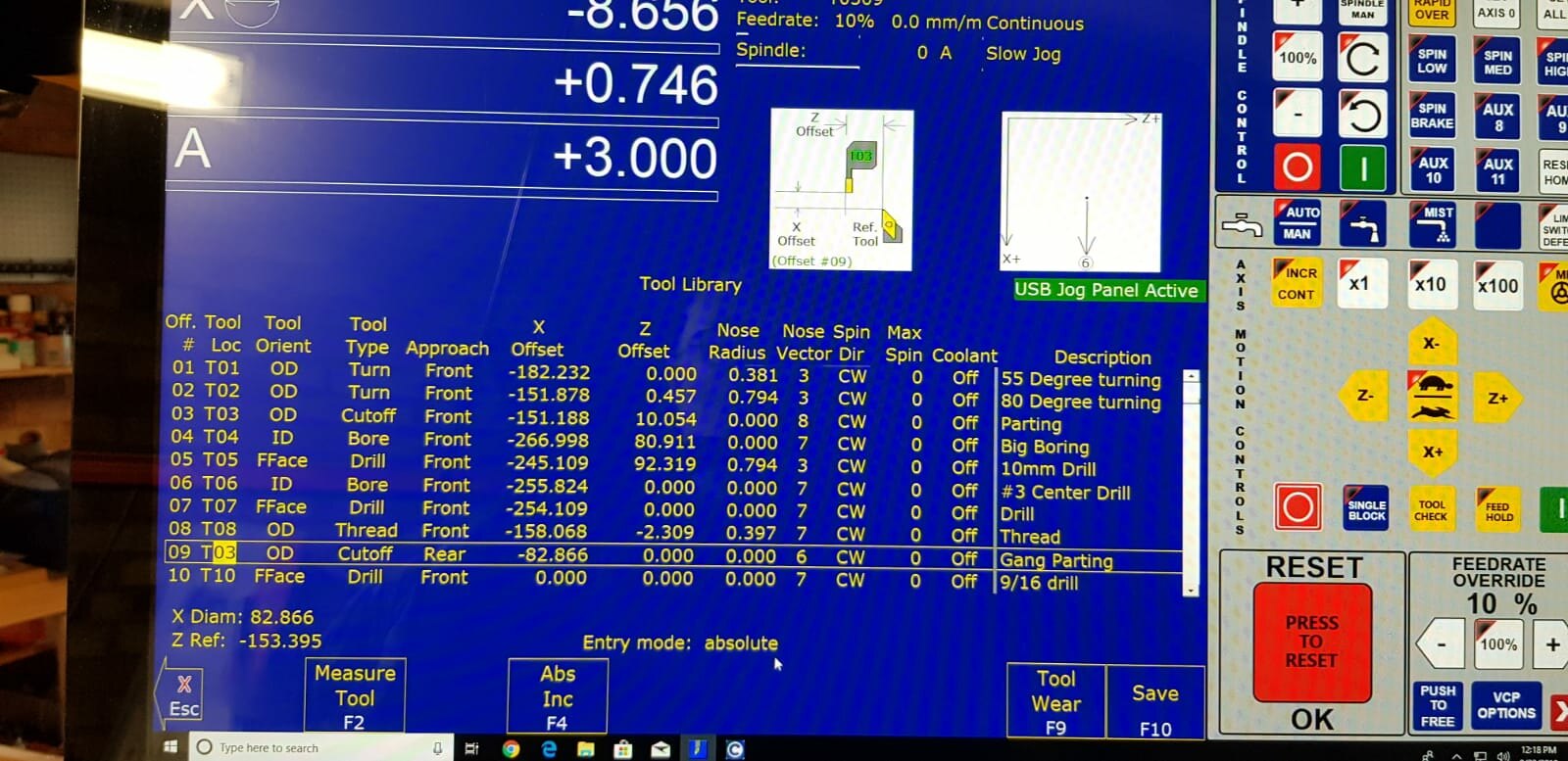
Any help appreciated before I go and spend on a gang tool setup.
Thanks
First thing, set parameter for Gang Tooling = 1. So now I have rear as an option.
The problem that I have is that the X never flips over. First, below is a pic of my lathe's orientation. Ignore the temp nature of the gang tooling, just for visual representation. Tool turret at the bottom, gang at the top.
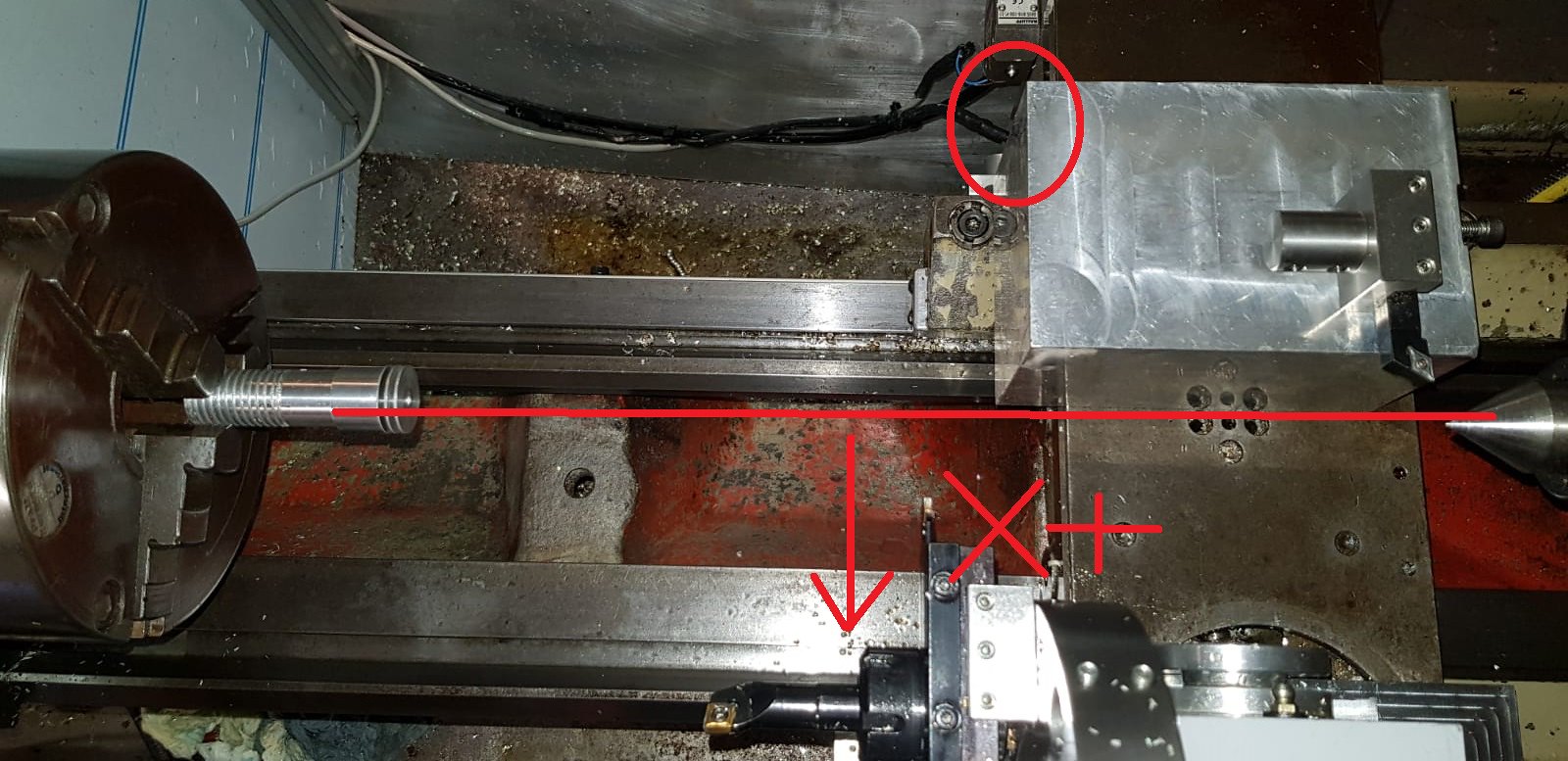
I home the machine to the home switch at the top (red circle) which means that the X is in its most positive direction. My offsets are all negative (basically my offsets are from machine 0, not sure if this is an issue.
I also noted that Parameter 1 allows a modification to the machine layout. Mine was parameter = 1. It says then to allow X to flip, add 2 to the amount (so use Parameter 1 = 3). I did this too, no change. Do I need to restart the system (Acorn) before these changes take effect?

I tried various options, tool 3 offset 9. What I did not try (another thread refers to it) was to bluff saying that its an ID tool, not OD. I tried Rear Approach, vector 6 and 8. The X doesnt switch over, no matter what I tried.
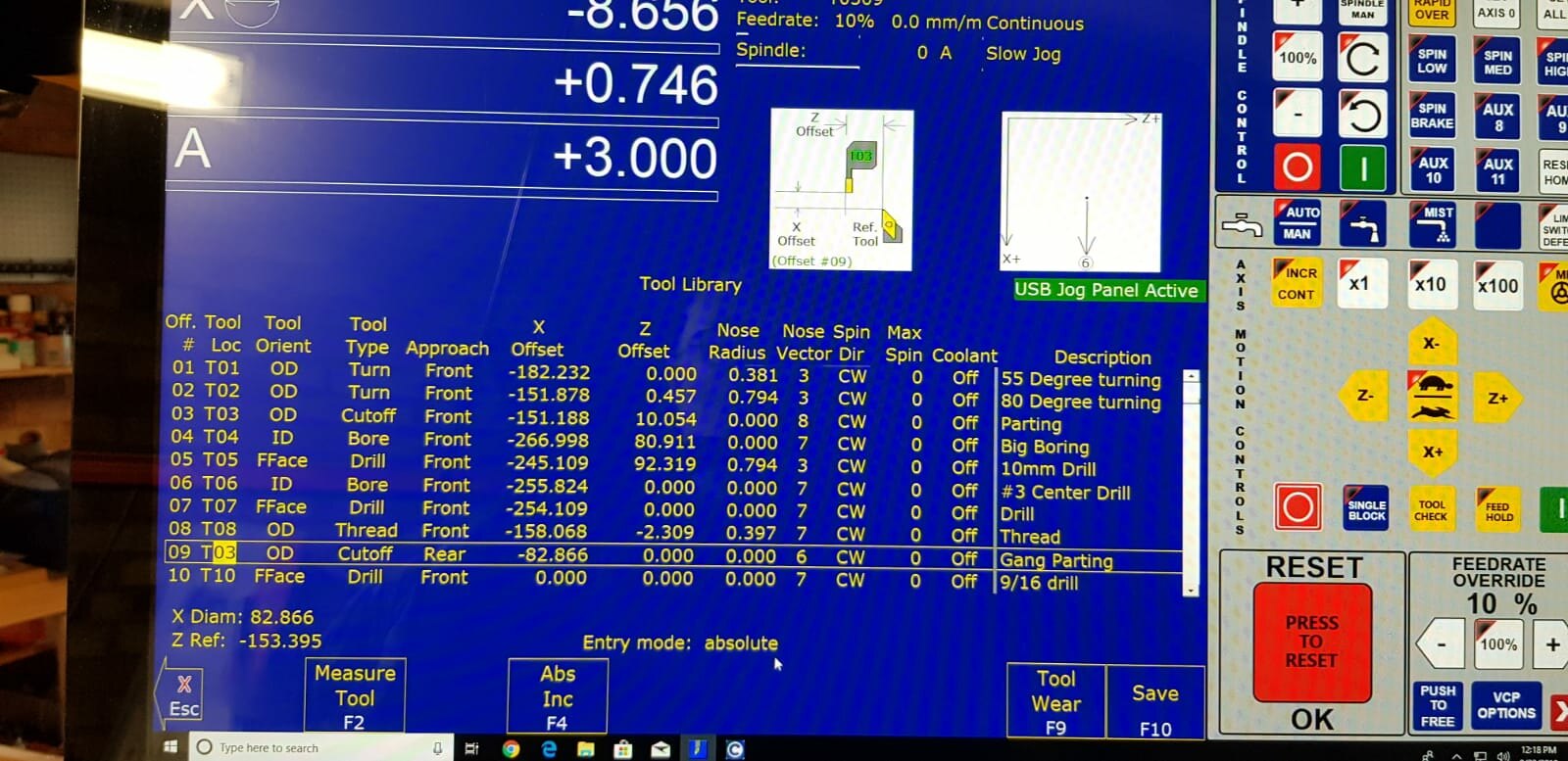
Any help appreciated before I go and spend on a gang tool setup.
Thanks
-
- Posts: 237
- Joined: Mon Nov 20, 2017 10:13 am
- Acorn CNC Controller: Yes
- Allin1DC CNC Controller: No
- Oak CNC controller: No
- CNC Control System Serial Number: none
- DC3IOB: No
- CNC11: Yes
- CPU10 or CPU7: Yes
- Location: Frenchville, PA
Re: ATC + Manual Gang
Chaz,
On a lathe Part X0.0 is set to the center of the spindle not machine home. This would be the problem. The X Diam is the diameter of the material you are touching the tool off of. For the turret (ATC) the X DIam will be a positive number. For the the gang tool approaching from the rear the X Diam will be a negative number. For cutting with the gang tool the X values will be negative because you are approaching from the rear which is the negative side of center line.
Parameter 1 was set correctly at 1 for you lathe with approaching from the front. Change back to 1.Chaz wrote: ↑Mon Sep 24, 2018 3:18 am I also noted that Parameter 1 allows a modification to the machine layout. Mine was parameter = 1. It says then to allow X to flip, add 2 to the amount (so use Parameter 1 = 3). I did this too, no change. Do I need to restart the system (Acorn) before these changes take effect?
Dana
When requesting support, please ALWAYS post a current report.
Need support? READ THIS POST first. http://centroidcncforum.com/viewtopic.php?f=60&t=1043
All Acorn Documentation is located here: viewtopic.php?f=60&t=3397
Answers to common questions: viewforum.php?f=63
and here viewforum.php?f=61
When requesting support, please ALWAYS post a current report.
Need support? READ THIS POST first. http://centroidcncforum.com/viewtopic.php?f=60&t=1043
All Acorn Documentation is located here: viewtopic.php?f=60&t=3397
Answers to common questions: viewforum.php?f=63
and here viewforum.php?f=61
-
- Posts: 392
- Joined: Thu Feb 08, 2018 7:57 am
- Acorn CNC Controller: No
- Allin1DC CNC Controller: No
- Oak CNC controller: No
- CNC Control System Serial Number: none
- DC3IOB: No
- CNC11: No
- CPU10 or CPU7: No
Re: ATC + Manual Gang
I'm confused.cnc_smith wrote: ↑Mon Sep 24, 2018 8:50 am Chaz,
On a lathe Part X0.0 is set to the center of the spindle not machine home. This would be the problem. The X Diam is the diameter of the material you are touching the tool off of. For the turret (ATC) the X DIam will be a positive number. For the the gang tool approaching from the rear the X Diam will be a negative number. For cutting with the gang tool the X values will be negative because you are approaching from the rear which is the negative side of center line.
Parameter 1 was set correctly at 1 for you lathe with approaching from the front. Change back to 1.Chaz wrote: ↑Mon Sep 24, 2018 3:18 am I also noted that Parameter 1 allows a modification to the machine layout. Mine was parameter = 1. It says then to allow X to flip, add 2 to the amount (so use Parameter 1 = 3). I did this too, no change. Do I need to restart the system (Acorn) before these changes take effect?
I agree that your 'relative' X 0 is the middle. The tool offsets give me that. When I use tool 1, at 10mm diameter, I get a 10mm wide part and so forth.
In this case, I am using Z = 0 for Machine coordinates. Is this still an issue?
For the Parameter 1 value, arent we trying to use both side (front and rear approaches)?
-
- Posts: 392
- Joined: Thu Feb 08, 2018 7:57 am
- Acorn CNC Controller: No
- Allin1DC CNC Controller: No
- Oak CNC controller: No
- CNC Control System Serial Number: none
- DC3IOB: No
- CNC11: No
- CPU10 or CPU7: No
Re: ATC + Manual Gang
Ive reread your response.
I agree with one side being positive, another negative.
My point is if I tell it to go 'larger' (from small to large) diameter, with my ATC, it moves X+ direction.
For the Gang, it needs to move X- to get the diameter larger, how / where is this flipped over?
I tried to use different offset values, all it does (positive and negative) is mess with the resulting diameter, motion remains X + downwards, irrespective of approach direction or nose vectors. The only thing I did not try was an ID tool or actually reboot the board after the changes.
I agree with one side being positive, another negative.
My point is if I tell it to go 'larger' (from small to large) diameter, with my ATC, it moves X+ direction.
For the Gang, it needs to move X- to get the diameter larger, how / where is this flipped over?
I tried to use different offset values, all it does (positive and negative) is mess with the resulting diameter, motion remains X + downwards, irrespective of approach direction or nose vectors. The only thing I did not try was an ID tool or actually reboot the board after the changes.